A form in which piperazine is commonly available industrially is as the hexahydrate, C4H10N2. 6H2O, which melts at 44 °C and boils at 125–130 °C.[3]
Piperazine readily absorbs water and carbon dioxide from the air. Although many piperazine derivatives occur naturally, piperazine itself can be synthesized by reacting alcoholic ammonia with 1,2-dichloroethane, by the action of sodium and ethylene glycol on ethylene diaminehydrochloride, or by reduction of pyrazine with sodium in ethanol.
A form in which piperazine is commonly available industrially is as the hexahydrate, C4H10N2. 6H2O, which melts at 44 °C and boils at 125–130 °C.[3]
Two common salts in the form of which piperazine is usually prepared for pharmaceutical or veterinary purposes are the citrate, 3C4H10N2.2C6H8O7 (i.e. containing 3 molecules of piperazine to 2 molecules of citric acid), and the adipate, C4H10N2.C6H10O4 (containing 1 molecule each of piperazine and adipic acid).[3]

Simplified absorption column. Typical operating range: 35-50 °C and 5-205 atm of absolute pressure
https://en.wikipedia.org/wiki/Piperazine
Pipobroman (trade names Vercite, Vercyte) is an anti-cancer drug that probably acts as an alkylating agent.[1] It is marketed in France and Italy.[2]
Pipobroman

L01AX02 (WHO) Identifiers
show
IUPAC nameCAS Number
54-91-1

4842IUPHAR/BPS
7271DrugBank
DB00236

4676

6Q99RDT97RKEGG
D00467

CHEBI:8242ChEMBL
ChEMBL1585

DTXSID7023485

Interactive image
show
SMILES
show
InChI (verify)
https://en.wikipedia.org/wiki/Pipobroman
Tralomethrin is a pyrethroid insecticide.
Tralomethrin has potent insecticidal properties; it kills by modifying the gating kinetics of the sodium channels in neurons, increasing the length of time the channel remains open after a stimulus, thereby depolarizing the neuron for a longer period of time. This leads to uncontrolled spasming, paralysis, and eventual death. Insects with certain mutations in their sodium channel gene may be resistant to tralomethrin and other similar insecticides.

(1R,3S)-2,2-Dimethyl-3-(1,2,2,2-tetrabromoethyl)-1-cyclopropanecarboxylic acid [(S)-cyano-[3-(phenoxy)phenyl]methyl] ester
Identifiers
CAS Number
66841-25-6

3D model (JSmol)
Interactive imageChemSpider
43788


C18413

PubChem CID
48132UNII
W2Z59VSQ0O

CompTox Dashboard (EPA)
DTXSID0024343

show
InChI
show
SMILESProperties
Chemical formulaC22H19Br4NO3Molar mass665.014 g·mol−1AppearanceColorless liquidDensity1.70 g/cm3 at 20 °CMelting point138 to 148 °C (280 to 298 °F; 411 to 421 K)Boiling point594 °C (1,101 °F; 867 K)
Except where otherwise noted, data are given for materials in their standard state (at 25 °C [77 °F], 100 kPa).



Infobox references
Effectiveness[edit]
Tralomethrin is also effective against most members of class Arachnida as well as insects, in addition studies by the EPA on the ecotoxicity of tralomethrin shows results as follows:
Tralomethrin Ecotoxicity
Organism Group Effects Noted
Aquatic plants Accumulation
Crustaceans Intoxication, Population
Fish Accumulation, Mortality, Population
Insects Mortality, Population
Molluscs Intoxication
Zooplankton Intoxication, Mortality, Population
Impact on human health[edit]
Tralomethrin is a pyrethroid insecticide. The symptoms of poisoning with pyrethroid compounds are all alike:Irritation of skin and eyes.
Irritability to sound or touch, abnormal facial sensation, sensation of prickling, tingling or creeping on skin, numbness.
Headache, dizziness, nausea, vomiting, diarrhea, excessive salivation, fatigue.
In severe cases: fluid in the lungs and muscle twitching may develop. Seizures may occur and are more common with more toxic cyano-pyrethroids.
https://en.wikipedia.org/wiki/Tralomethrin
Bromobenzyl cyanide (BBC) is an obsolete lachrymatory agent[1] introduced in World War I by the Allied Powers. When implemented in World War I, it revolutionized the use of tear agents due to their extreme potency. BBC is toxic like chlorine gas.[2]

(RS)-2-bromo-2-phenylacetonitrile
Other names
α-bromobenzyl cyanide
Identifiers
CAS Number
5798-79-8

3D model (JSmol)
Interactive imageChemSpider
20715


PubChem CID
22044UNII
7JP1R2F6C6

show
InChI
show
SMILESProperties
Chemical formulaC8H6BrN Molar mass196.04 g mol−1
Except where otherwise noted, data are given for materials in their standard state (at 25 °C [77 °F], 100 kPa).



Infobox references
https://en.wikipedia.org/wiki/Bromobenzyl_cyanide
CR gas or dibenzoxazepine (chemical name dibenz[b,f][1,4]oxazepine, is an incapacitating agent and a lachrymatory agent. CR was developed by the British Ministry of Defence as a riot control agent in the late 1950s and early 1960s. A report from the Porton Down laboratories described exposure as "like being thrown blindfolded into a bed of stinging nettles", and it earned the nickname "firegas".[1][2]
In its effects, the CR gas is very similar (but twice as potent) to o-chlorobenzylidene malononitrile CS gas, even though there is little structural resemblance between the two. For example, 2 mg of dry CR cause skin redness in 10 min, 5 mg cause burning and erythrema, 20 mg- strong pain. Water usually amplifies the pain effect of CR on skin. CR aerosols cause irritation as 0.0002 mg/L, which becomes intolerable at 0.003 mg/L. The lethal dose of CR through air inhalation is LD50 = 350 mg·min/L.[3]


Dibenzo[b,f][1,4]oxazepine
Identifiers
CAS Number
257-07-8

3D model (JSmol)
Interactive imageChEMBL
ChEMBL1085100

8858


IUPHAR/BPS
6472
PubChem CID
9213UNII
C1Q77A87V1

CompTox Dashboard (EPA)
DTXSID8059764

show
InChI
show
SMILESProperties
Chemical formulaC13H9NO Molar mass195.22 g/mol Density1.160±0.10 g/cm3Melting point73 °C (163 °F; 346 K)
Except where otherwise noted, data are given for materials in their standard state (at 25 °C [77 °F], 100 kPa).



Infobox references
https://en.wikipedia.org/wiki/CR_gas
Oxazepines are a family of unsaturated heterocycles containing seven atoms, with a nitrogen replacing a carbon at one position and with an oxygen replacing a carbon at one position.
See also[edit]Azepine
Benzazepines
Diazepine
Oxepin
Borepin
CR gas (dibenzoxazepine)
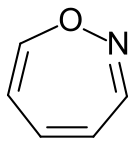
1,2-Oxazepine, one of the isomers of oxazepineNamesIUPAC name
1,2-OxazepineIdentifiers
CAS Number
1,2-: 291-79-2

1,4-: 292-10-4
3D model (JSmol)
1,2-: Interactive image
1,4-: Interactive imageChemSpider
1,2-: 11418660

PubChem CID
1,2-: 13781592
1,4-: 17860191
show
InChI
show
SMILESProperties
Chemical formulaC5H7NOMolar mass97.117 g·mol−1
Except where otherwise noted, data are given for materials in their standard state (at 25 °C [77 °F], 100 kPa).
Infobox references
https://en.wikipedia.org/wiki/Oxazepine
Azepines are unsaturated heterocycles of seven atoms, with a nitrogen replacing a carbon at one position.
See also[edit]Azepane
Benzazepines
Diazepine
Oxepin
Borepin


NamesIUPAC name
AzepineOther names
AzacycloheptatrieneIdentifiers
CAS Number
291-69-0

3D model (JSmol)
Interactive imageChemSpider
4953941

PubChem CID
6451476
CompTox Dashboard (EPA)
DTXSID50183352

show
InChI
show
SMILESProperties
Chemical formulaC6H7NMolar mass93.129 g·mol−1
Except where otherwise noted, data are given for materials in their standard state (at 25 °C [77 °F], 100 kPa).



Infobox references
https://en.wikipedia.org/wiki/Azepine
1-Bromonaphthalene is an organic compound with the formula C10H7Br.
It is one of two isomeric bromonaphthalenes, the other being 2-bromonaphthalene. Under normal conditions, the substance is a colorless liquid.
NamesPreferred IUPAC name
Other names
Identifiers
- 90-11-9 3D model (JSmol)ChemSpiderECHA InfoCard100.001.787 EC NumberMeSHC108222
- 201-965-2
PubChem CIDUNII- 976Y53P08P CompTox Dashboard (EPA)PropertiesC10H7Br Molar mass207.07 Appearancecolorless liquidDensity1.48 g/mLMelting point1-2 ºCBoiling point132–135 °C at 12 mm; 145–148 °C at 20 mmExcept where otherwise noted, data are given for materials in their standard state (at 25 °C [77 °F], 100 kPa).
https://en.wikipedia.org/wiki/1-Bromonaphthalene
Vinyl bromide is a simple vinyl halide. It is a colorless liquid. It is produced from ethylene dibromide. It is mainly used as a comonomer to confer fire retardant properties to acrylate polymers.[2]
NamesPreferred IUPAC name
Other names
1-Bromoethene
Bromoethylene
1-Bromoethylene
Monobromoethene
Monobromoethylene
Identifiers
- 593-60-2 3D model (JSmol)ChEBIChemSpider
- 11151
ECHA InfoCard100.008.911 EC Number
KEGG- 209-800-6
- C19184 PubChem CIDRTECS numberUNII
- KU8400000
- 83NRW59KFY
UN number1085
CompTox Dashboard (EPA)PropertiesC2H3Br Molar mass106.95 g/mol AppearanceColorless gasOdorpleasant[1]Density1.525 g/cm3 at boiling point (liquid)1.4933 g/cm3 at 20 °C
Melting point−137.8 °C (−216.0 °F; 135.3 K)Boiling point15.8 °C (60.4 °F; 288.9 K)Insolublelog P1.57Vapor pressure206.8 kPa at 37.8 °CHazardsGHS labelling:DangerH220, H350P201, P202, P210, P281, P308+P313, P377, P381, P403, P405, P501NFPA 704(fire diamond)Flash point5 °C (41 °F; 278 K)530 °C (986 °F; 803 K)Explosive limits9%-15%[1]NIOSH (US health exposure limits):
PEL(Permissible)none[1]REL(Recommended)Ca[1]IDLH (Immediate danger)N.D.[1]Supplementary data pageVinyl bromide (data page)Except where otherwise noted, data are given for materials in their standard state (at 25 °C [77 °F], 100 kPa).
- 11151
https://en.wikipedia.org/wiki/Vinyl_bromide
Vinyl chloride is an organochloride with the formula H2C=CHCl. It is also called vinyl chloride monomer (VCM) or chloroethene. This colorless compound is an important industrial chemical chiefly used to produce the polymer polyvinyl chloride (PVC). About 13 billion kilograms are produced annually. VCM is among the top twenty largest petrochemicals(petroleum-derived chemicals) in world production.[2] The United States currently remains the largest VCM manufacturing region because of its low-production-cost position in chlorine and ethylene raw materials. China is also a large manufacturer and one of the largest consumers of VCM.[3] Vinyl chloride is a gas with a sweet odor. It is highly toxic, flammable, and carcinogenic. It can be formed in the environment when soil organisms break down chlorinated solvents. Vinyl chloride that is released by industries or formed by the breakdown of other chlorinated chemicals can enter the air and drinking water supplies. Vinyl chloride is a common contaminant found near landfills.[4] In the past VCM was used as a refrigerant.[5]
NamesPreferred IUPAC name
Other names
VCM
Chloroethylene
Refrigerant-1140
Identifiers
- 75-01-4 3D model (JSmol)1731576ChEBI
- CHEBI:28509
ChEMBLChemSpider
- 6098
ECHA InfoCard100.000.756 EC Number
100541KEGG- 200-831-0
- C06793 PubChem CIDRTECS numberUNII
- KU9625000
- WD06X94M2D
UN number1086
CompTox Dashboard (EPA)PropertiesC2H3ClMolar mass62.50 g·mol−1AppearanceColorless gasOdorpleasant[1]Density0.911 g/mlMelting point−153.8 °C (−244.8 °F; 119.3 K)Boiling point−13.4 °C (7.9 °F; 259.8 K)2.7 g/L (0.0432 mol/L)Vapor pressure2580 mm. of mercury 20 °C (68 °F)-35.9·10−6 cm3/molThermochemistryHeat capacity (C)0.8592 J/K/g (gas)
0.9504 J/K/g (solid)Std enthalpy of−94.12 kJ/mol (solid)HazardsGHS labelling:
formation(ΔfH⦵298)DangerH220, H350P201, P202, P210, P281, P308+P313, P377, P381, P403, P405, P501NFPA 704(fire diamond)Flash point−61 °C (−78 °F; 212 K)Explosive limits3.6–33%[1]NIOSH (US health exposure limits):
PEL(Permissible)TWA 1 ppm C 5 ppm [15-minute][1]REL(Recommended)Ca[1]IDLH (Immediate danger)Ca [N.D.][1]Except where otherwise noted, data are given for materials in their standard state (at 25 °C [77 °F], 100 kPa).
- 6098
- CHEBI:28509
https://en.wikipedia.org/wiki/Vinyl_chloride
Continuous distillation, a form of distillation, is an ongoing separation in which a mixture is continuously (without interruption) fed into the process and separated fractions are removed continuously as output streams. Distillation is the separation or partial separation of a liquid feed mixture into components or fractions by selective boiling (or evaporation) and condensation. The process produces at least two output fractions. These fractions include at least one volatiledistillate fraction, which has boiled and been separately captured as a vapor condensed to a liquid, and practically always a bottoms (or residuum) fraction, which is the least volatile residue that has not been separately captured as a condensed vapor.
An alternative to continuous distillation is batch distillation, where the mixture is added to the unit at the start of the distillation, distillate fractions are taken out sequentially in time (one after another) during the distillation, and the remaining bottoms fraction is removed at the end. Because each of the distillate fractions are taken out at different times, only one distillate exit point (location) is needed for a batch distillation and the distillate can just be switched to a different receiver, a fraction-collecting container. Batch distillation is often used when smaller quantities are distilled. In a continuous distillation, each of the fraction streams is taken simultaneously throughout operation; therefore, a separate exit point is needed for each fraction. In practice when there are multiple distillate fractions, the distillate exit points are located at different heights on a fractionating column. The bottoms fraction can be taken from the bottom of the distillation column or unit, but is often taken from a reboiler connected to the bottom of the column.
Each fraction may contain one or more components (types of chemical compounds). When distilling crude oil or a similar feedstock, each fraction contains many components of similar volatility and other properties. Although it is possible to run a small-scale or laboratory continuous distillation, most often continuous distillation is used in a large-scale industrial process.
Industrial application[edit]
Distillation is one of the unit operations of chemical engineering.[1][2] Continuous distillation is used widely in the chemical process industries where large quantities of liquids have to be distilled.[3][4][5] Such industries are the natural gas processing, petrochemical production, coal tar processing, liquor production, liquified airseparation, hydrocarbon solvents production, cannabinoid separation and similar industries, but it finds its widest application in petroleum refineries. In such refineries, the crude oil feedstock is a very complex multicomponent mixture that must be separated and yields of pure chemical compounds are not expected, only groups of compounds within a relatively small range of boiling points, which are called fractions. These fractions are the origin of the term fractional distillation or fractionation. It is often not worthwhile separating the components in these fractions any further based on product requirements and economics.
Industrial distillation is typically performed in large, vertical cylindrical columns (as shown in images 1 and 2) known as "distillation towers" or "distillation columns" with diameters ranging from about 65 centimeters to 11 meters and heights ranging from about 6 meters to 60 meters or more.
Principle[edit]
The principle for continuous distillation is the same as for normal distillation: when a liquid mixture is heated so that it boils, the composition of the vapor above the liquid differs from the liquid composition. If this vapor is then separated and condensed into a liquid, it becomes richer in the lower boiling point component(s) of the original mixture.
This is what happens in a continuous distillation column. A mixture is heated up, and routed into the distillation column. On entering the column, the feed starts flowing down but part of it, the component(s) with lower boiling point(s), vaporizes and rises. However, as it rises, it cools and while part of it continues up as vapor, some of it (enriched in the less volatile component) begins to descend again.
Image 3 depicts a simple continuous fractional distillation tower for separating a feed stream into two fractions, an overhead distillate product and a bottoms product. The "lightest" products (those with the lowest boiling point or highest volatility) exit from the top of the columns and the "heaviest" products (the bottoms, those with the highest boiling point) exit from the bottom of the column. The overhead stream may be cooled and condensed using a water-cooled or air-cooled condenser. The bottoms reboiler may be a steam-heated or hot oil-heated heat exchanger, or even a gas or oil-fired furnace.
In a continuous distillation, the system is kept in a steady state or approximate steady state. Steady state means that quantities related to the process do not change as time passes during operation. Such constant quantities include feed input rate, output stream rates, heating and cooling rates, reflux ratio, and temperatures, pressures, and compositions at every point (location). Unless the process is disturbed due to changes in feed, heating, ambient temperature, or condensing, steady state is normally maintained. This is also the main attraction of continuous distillation, apart from the minimum amount of (easily instrumentable) surveillance; if the feed rate and feed composition are kept constant, product rate and quality are also constant. Even when a variation in conditions occurs, modern process control methods are commonly able to gradually return the continuous process to another steady state again.
Since a continuous distillation unit is fed constantly with a feed mixture and not filled all at once like a batch distillation, a continuous distillation unit does not need a sizable distillation pot, vessel, or reservoir for a batch fill. Instead, the mixture can be fed directly into the column, where the actual separation occurs. The height of the feed point along the column can vary on the situation and is designed so as to provide optimal results. See McCabe–Thiele method.
A continuous distillation is often a fractional distillation and can be a vacuum distillation or a steam distillation.
Design and operation[edit]
Design and operation of a distillation column depends on the feed and desired products. Given a simple, binary component feed, analytical methods such as the McCabe–Thiele method[5][6][7] or the Fenske equation[5] can be used to assist in the design. For a multi-component feed, computerized simulation models are used both for design and subsequently in operation of the column as well. Modeling is also used to optimize already erected columns for the distillation of mixtures other than those the distillation equipment was originally designed for.
When a continuous distillation column is in operation, it has to be closely monitored for changes in feed composition, operating temperature and product composition. Many of these tasks are performed using advanced computer control equipment.
Column feed[edit]
The column can be fed in different ways. If the feed is from a source at a pressure higher than the distillation column pressure, it is simply piped into the column. Otherwise, the feed is pumped or compressed into the column. The feed may be a superheated vapor, a saturated vapor, a partially vaporized liquid-vapor mixture, a saturated liquid (i.e., liquid at its boiling point at the column's pressure), or a sub-cooled liquid. If the feed is a liquid at a much higher pressure than the column pressure and flows through a pressure let-down valve just ahead of the column, it will immediately expand and undergo a partial flash vaporization resulting in a liquid-vapor mixture as it enters the distillation column.
Improving separation[edit]
Although small size units, mostly made of glass, can be used in laboratories, industrial units are large, vertical, steel vessels (see images 1 and 2) known as "distillation towers" or "distillation columns". To improve the separation, the tower is normally provided inside with horizontal plates or trays as shown in image 5, or the column is packed with a packing material. To provide the heat required for the vaporization involved in distillation and also to compensate for heat loss, heat is most often added to the bottom of the column by a reboiler, and the purity of the top product can be improved by recycling some of the externally condensed top product liquid as reflux. Depending on their purpose, distillation columns may have liquid outlets at intervals up the length of the column as shown in image 4.
Reflux[edit]
Large-scale industrial fractionation towers use reflux to achieve more efficient separation of products.[3][5] Reflux refers to the portion of the condensed overhead liquid product from a distillation tower that is returned to the upper part of the tower as shown in images 3 and 4. Inside the tower, the downflowing reflux liquid provides cooling and partial condensation of the upflowing vapors, thereby increasing the efficacy of the distillation tower. The more reflux that is provided, the better is the tower's separation of the lower boiling from the higher boiling components of the feed. A balance of heating with a reboiler at the bottom of a column and cooling by condensed reflux at the top of the column maintains a temperature gradient (or gradual temperature difference) along the height of the column to provide good conditions for fractionating the feed mixture. Reflux flows at the middle of the tower are called pumparounds.
Changing the reflux (in combination with changes in feed and product withdrawal) can also be used to improve the separation properties of a continuous distillation column while in operation (in contrast to adding plates or trays, or changing the packing, which would, at a minimum, require quite significant downtime).
Plates or trays[edit]
Distillation towers (such as in images 3 and 4) use various vapor and liquid contacting methods to provide the required number of equilibrium stages. Such devices are commonly known as "plates" or "trays".[8] Each of these plates or trays is at a different temperature and pressure. The stage at the tower bottom has the highest pressure and temperature. Progressing upwards in the tower, the pressure and temperature decreases for each succeeding stage. The vapor–liquid equilibrium for each feed component in the tower reacts in its unique way to the different pressure and temperature conditions at each of the stages. That means that each component establishes a different concentration in the vapor and liquid phases at each of the stages, and this results in the separation of the components. Some example trays are depicted in image 5. A more detailed, expanded image of two trays can be seen in the theoretical plate article. The reboiler often acts as an additional equilibrium stage.
If each physical tray or plate were 100% efficient, then the number of physical trays needed for a given separation would equal the number of equilibrium stages or theoretical plates. However, that is very seldom the case. Hence, a distillation column needs more plates than the required number of theoretical vapor–liquid equilibrium stages.
Packing[edit]
Another way of improving the separation in a distillation column is to use a packing material instead of trays. These offer the advantage of a lower pressure drop across the column (when compared to plates or trays), beneficial when operating under vacuum. If a distillation tower uses packing instead of trays, the number of necessary theoretical equilibrium stages is first determined and then the packing height equivalent to a theoretical equilibrium stage, known as the height equivalent to a theoretical plate (HETP), is also determined. The total packing height required is the number of theoretical stages multiplied by the HETP.
This packing material can either be random dumped packing such as Raschig rings or structured sheet metal. Liquids tend to wet the surface of the packing and the vapors pass across this wetted surface, where mass transfer takes place. Unlike conventional tray distillation in which every tray represents a separate point of vapor–liquid equilibrium, the vapor–liquid equilibrium curve in a packed column is continuous. However, when modeling packed columns it is useful to compute a number of theoretical plates to denote the separation efficiency of the packed column with respect to more traditional trays. Differently shaped packings have different surface areas and void space between packings. Both of these factors affect packing performance.
Another factor in addition to the packing shape and surface area that affects the performance of random or structured packing is liquid and vapor distribution entering the packed bed. The number of theoretical stages required to make a given separation is calculated using a specific vapor to liquid ratio. If the liquid and vapor are not evenly distributed across the superficial tower area as it enters the packed bed, the liquid to vapor ratio will not be correct in the packed bed and the required separation will not be achieved. The packing will appear to not be working properly. The height equivalent to a theoretical plate (HETP) will be greater than expected. The problem is not the packing itself but the mal-distribution of the fluids entering the packed bed. Liquid mal-distribution is more frequently the problem than vapor. The design of the liquid distributors used to introduce the feed and reflux to a packed bed is critical to making the packing perform at maximum efficiency. Methods of evaluating the effectiveness of a liquid distributor can be found in references.[9][10]
Overhead system arrangements[edit]
Images 4 and 5 assume an overhead stream that is totally condensed into a liquid product using water or air-cooling. However, in many cases, the tower overhead is not easily condensed totally and the reflux drum must include a vent gas outlet stream. In yet other cases, the overhead stream may also contain water vapor because either the feed stream contains some water or some steam is injected into the distillation tower (which is the case in the crude oil distillation towers in oil refineries). In those cases, if the distillate product is insoluble in water, the reflux drum may contain a condensed liquid distillate phase, a condensed water phase and a non-condensible gas phase, which makes it necessary that the reflux drum also have a water outlet stream.
Multicomponent distillation[edit]
Beside fractional distillation, that is mainly used for crude oil refining, multicomponent mixtures are usually processed in order to purify their single components by means of a series of distillation columns, i.e. the distillation train.
Distillation train[edit]
A distillation train is defined by a sequence of distillation columns arranged in series or in parallel whose aim is the multicomponent mixtures purification.
Process intensifying alternatives[edit]
The Dividing Wall Column unit is most common process-intensifying unit related to distillation. In particular, it is the arrangement in a single column shell of the Petlyuk configuration[11] that has been proved to be thermodynamically equivalent.[12]
Examples[edit]
Continuous distillation of crude oil[edit]
Petroleum crude oils contain hundreds of different hydrocarbon compounds: paraffins, naphthenes and aromatics as well as organic sulfur compounds, organic nitrogen compounds and some oxygen-containing hydrocarbons such as phenols. Although crude oils generally do not contain olefins, they are formed in many of the processes used in a petroleum refinery.[13]
The crude oil fractionator does not produce products having a single boiling point; rather, it produces fractions having boiling ranges.[13][14] For example, the crude oil fractionator produces an overhead fraction called "naphtha" which becomes a gasoline component after it is further processed through a catalytic hydrodesulfurizer to remove sulfur and a catalytic reformer to reform its hydrocarbon molecules into more complex molecules with a higher octane rating value.
The naphtha cut, as that fraction is called, contains many different hydrocarbon compounds. Therefore, it has an initial boiling point of about 35 °C and a final boiling point of about 200 °C. Each cut produced in the fractionating columns has a different boiling range. At some distance below the overhead, the next cut is withdrawn from the side of the column and it is usually the jet fuel cut, also known as a kerosene cut. The boiling range of that cut is from an initial boiling point of about 150 °C to a final boiling point of about 270 °C, and it also contains many different hydrocarbons. The next cut further down the tower is the diesel oil cut with a boiling range from about 180 °C to about 315 °C. The boiling ranges between any cut and the next cut overlap because the distillation separations are not perfectly sharp. After these come the heavy fuel oil cuts and finally the bottoms product, with very wide boiling ranges. All these cuts are processed further in subsequent refining processes.
Continuous distillation of cannabis concentrates[edit]
A typical application for distilling cannabis concentrates is butane hash oil (BHO). Short path distillation is a popular method due to the short residence time which allows for minimal thermal stress to the concentrate. In other distillation methods such as circulation, falling film and column distillation the concentrate would be damaged from the long residence times and high temperatures that must be applied.
See also[edit]
- Azeotropic distillation
- Extractive distillation
- Fractional distillation
- Fractionating column
- Steam distillation
- Short path distillation
https://en.wikipedia.org/wiki/Continuous_distillation
The term structured packing refers to a range of specially designed materials for use in absorption and distillation columns and chemical reactors. Structured packings typically consist of thin corrugated metal plates or gauzes arranged in a way that force fluids to take complicated paths through the column, thereby creating a large surface area for contact between different phases.
Structured packing is formed from corrugated sheets of perforated embossed metal, plastic (including PTFE) or wire gauze. The result is a very open honeycomb structure with inclined flow channels giving a relatively high surface area but with very low resistance to gas flow. The surface enhancements have been chosen to maximize liquid spreading. These characteristics tend to show significant performance benefits in low pressure and low irrigation rate applications.[1]
History[edit]
Structured packings have been established for several decades. The first generation of structured packing arose in the early 1940s. In 1953, a patented packing appeared named Panapak, made of a wavy-form expanded metal sheet. The packing was not successful, due to maldistribution and lack of good marketing. The second generation appeared at the end of the 1950s, with highly efficient wire mesh packings, such as Goodloe, Hyperfil and Koch-Sulzer. Until the 1970s, due to their low pressure drop per theoretical stage, those packings were the most widely used in vacuum distillation. However, high cost, low capacity and high sensitivity to solids have prevented wider utilization of wire mesh packings.[citation needed]
Corrugated structured packings, introduced by Sulzer by the end of the 1970s, marked the third generation of structured packed columns. These packings offer high capacity, lower cost, and less sensitivity to solids, while keeping a high performance. Popularity of the packings grew in the 1980s, particularly for revamps in oil and petrochemical plants. These structured packings, made of corrugated metal sheets, had their surfaces treated, chemically or mechanically, in order to enhance their wettability. Consequently, the packings' wetted area increased, improving performance. In 1994, a new geometry was developed, and called Optiflow. Later, in 1999, an improved structure of corrugated sheet packings, the MellapackPlus, was developed based on CFD simulations and experiment. This new structure, compared with conventional Mellapak, has a lowered pressure drop and maximum useful capacity could be extended up to 50%.[citation needed]
Varieties[edit]
Structured packing is manufactured in a wide range of sizes by varying the crimp altitude. Packing surface ranges from 50 m²/m³ (lowest efficiency, highest capacity) to 750 m²/m³ (highest efficiency, lowest capacity).
Applications[edit]
Typical applications include vacuum and atmospheric crude oil fractionators, FCC main fractionators and TEG contactors. The separation of mono-, di- and triethanolamine, conducted under vacuum, may also utilize structured packing, owing to its relatively low pressure drop. Tall oil fractionation, the process of separating fatty acids from rosin acids and pitch obtained as a by-product of the Kraft process of wood pulp manufacture, also utilizes structured packing. The packing additionally finds use in the manufacture of styrene monomer and the dehydration of glycol in natural gas processing.[2]
Structured packing also finds use in the equipment/processes below:
- Air separation[3][4]
- Cyclohexanone/Cyclohexanol separation[3]
- Xylene splitters[3]
- CO2 absorbers[3]
- H2S absorbers[3]
- Ethylene oxide absorbers[3]
- Acrylonitrile absorbers[3]
- Oleo Chemicals [1]
- Fine Chemicals [2]
Advantages[edit]
Structured packing offers the following advantages as compared to the use of random packing and trays:
- Lower pressure drop[2][5]
- Higher efficiency (given the same tower height)[2][5]
- Higher capacity[2][5]
- Reduced liquid hold-up[2]
Disadvantages[edit]
Structured packing offers the following disadvantages as compared to the use of random packing and trays:
- Cost[5]
- Greater sensitivity to maldistribution[citation needed]
See also[edit]
https://en.wikipedia.org/wiki/Structured_packing
A rotary evaporator[1] (rotovap) is a device used in chemical laboratories for the efficient and gentle removal of solventsfrom samples by evaporation. When referenced in the chemistry research literature, description of the use of this technique and equipment may include the phrase "rotary evaporator", though use is often rather signaled by other language (e.g., "the sample was evaporated under reduced pressure").
Rotary evaporators are also used in molecular cooking for the preparation of distillates and extracts.
A simple rotary evaporator system was invented by Lyman C. Craig.[2] It was first commercialized by the Swiss company Büchi in 1957. Walter Büchi developed a world first commercial rotary evaporator, which separates substances with different boiling points, and greatly simplifies work in research laboratories.[citation needed] In research the most common form is the 1L bench-top unit, whereas large scale (e.g., 20L-50L) versions are used in pilot plants in commercial chemical operations.
Design[edit]
The main components of a rotary evaporator are:
- A motor unit that rotates the evaporation flask or vial containing the user's sample.
- A vapor duct that is the axis for sample rotation, and is a vacuum-tight conduit for the vapor being drawn off the sample.
- A vacuum system, to substantially reduce the pressure within the evaporator system.
- A heated fluid bath (generally water) to heat the sample.
- A condenser with either a coil passing coolant, or a "cold finger" into which coolant mixtures such as dry ice and acetone are placed.
- A condensate-collecting flask at the bottom of the condenser, to catch the distilling solvent after it re-condenses.
- A mechanical or motorized mechanism to quickly lift the evaporation flask from the heating bath.
The vacuum system used with rotary evaporators can be as simple as a water aspirator with a trap immersed in a cold bath (for non-toxic solvents), or as complex as a regulated mechanical vacuum pump with refrigerated trap. Glassware used in the vapor stream and condenser can be simple or complex, depending upon the goals of the evaporation, and any propensities the dissolved compounds might give to the mixture (e.g., to foam or "bump"). Commercial instruments are available that include the basic features, and various traps are manufactured to insert between the evaporation flask and the vapor duct. Modern equipment often adds features such as digital control of vacuum, digital display of temperature and rotational speed, and vapor temperature sensing.
Theory[edit]
Vacuum evaporators as a class function because lowering the pressure above a bulk liquid lowers the boiling points of the component liquids in it. Generally, the component liquids of interest in applications of rotary evaporation are research solvents that one desires to remove from a sample after an extraction, such as following a natural product isolation or a step in an organic synthesis. Liquid solvents can be removed without excessive heating of what are often complex and sensitive solvent-solute combinations.
Rotary evaporation is most often and conveniently applied to separate "low boiling" solvents such a n-hexane or ethyl acetate from compounds which are solid at room temperature and pressure. However, careful application also allows removal of a solvent from a sample containing a liquid compound if there is minimal co-evaporation (azeotropic behavior), and a sufficient difference in boiling points at the chosen temperature and reduced pressure.
Solvents with higher boiling points such as water (100 °C at standard atmospheric pressure, 760 torr or 1 bar), dimethylformamide (DMF, 153 °C at the same), or dimethyl sulfoxide (DMSO, 189 °C at the same), can also be evaporated if the unit's vacuum system is capable of sufficiently low pressure. (For instance, both DMF and DMSO will boil below 50 °C if the vacuum is reduced from 760 torr to 5 torr [from 1 bar to 6.6 mbar]) However, more recent developments are often applied in these cases (e.g., evaporation while centrifuging or vortexing at high speeds). Rotary evaporation for high boiling hydrogen bond-forming solvents such as water is often a last recourse, as other evaporation methods or freeze-drying (lyophilization) are available. This is partly due to the fact that in such solvents, the tendency to "bump" is accentuated. The modern centrifugal evaporation technologies are particularly useful when one has many samples to do in parallel, as in medium- to high-throughput synthesis now expanding in industry and academia.
Evaporation under vacuum can also, in principle, be performed using standard organic distillation glassware — i.e., without rotation of the sample. The key advantages in use of a rotary evaporator are
- That the centrifugal force and the frictional force between the wall of the rotating flask and the liquid sample result in the formation of a thin film of warm solvent being spread over a large surface.
- The forces created by the rotation suppress bumping. The combination of these characteristics and the conveniences built into modern rotary evaporators allow for quick, gentle evaporation of solvents from most samples, even in the hands of relatively inexperienced users. Solvent remaining after rotary evaporation can be removed by exposing the sample to even deeper vacuum, on a more tightly sealed vacuum system, at ambient or higher temperature (e.g., on a Schlenk lineor in a vacuum oven).
A key disadvantage in rotary evaporations, besides its single sample nature, is the potential of some sample types to bump, e.g. ethanol and water, which can result in loss of a portion of the material intended to be retained. Even professionals experience periodic mishaps during evaporation, especially bumping, though experienced users become aware of the propensity of some mixtures to bump or foam, and apply precautions that help to avoid most such events. In particular, bumping can often be prevented by taking homogeneous phases into the evaporation, by carefully regulating the strength of the vacuum (or the bath temperature) to provide for an even rate of evaporation, or, in rare cases, through use of added agents such as boiling chips (to make the nucleation step of evaporation more uniform). Rotary evaporators can also be equipped with further special traps and condenser arrays that are best suited to particular difficult sample types, including those with the tendency to foam or bump.
Safety[edit]
Possible hazards include implosions resulting from use of glassware that contains flaws, such as star-cracks. Explosions may occur from concentrating unstable impurities during evaporation, for example when rotavapping an ethereal solution containing peroxides. This can also occur when taking certain unstable compounds, such as organic azides and acetylides, nitro-containing compounds, molecules with strain energy, etc. to dryness.
Users of rotary evaporation equipment must take precautions to avoid contact with rotating parts, particularly entanglement of loose clothing, hair, or necklaces. Under these circumstances, the winding action of the rotating parts can draw the users into the apparatus resulting in breakage of glassware, burns, and chemical exposure. Extra caution must also be applied to operations with air reactive materials, especially when under vacuum. A leak can draw air into the apparatus and a violent reaction can occur.
See also[edit]
Principles | ![]() | |
---|---|---|
Industrial processes | ||
Laboratory methods | ||
Techniques |
https://en.wikipedia.org/wiki/Rotary_evaporator
Salt-effect distillation is a method of extractive distillation in which a salt is dissolved in the mixture of liquids to be distilled. The salt acts as a separating agent by raising the relative volatility of the mixture and by breaking any azeotropes that may otherwise form.
Setup[edit]
The salt is fed into the distillation column at a steady rate by adding it to the reflux stream at the top of the column. It dissolves in the liquid phase, and since it is non-volatile, flows out with the heavier bottoms stream. The bottoms are partially or completely evaporated to recover the salt for reuse. Yeah
Usage[edit]
Extractive distillation is more costly than ordinary fractional distillation due to costs associated with the recovery of the separating agent. One advantage of salt-effect distillation over other types of azeotropic distillation is the potential for reduced costs associated with energy usage. In addition, the salt ions have a greater effect on the volatility of the mixture to be distilled than other liquid separating agents. [1] Commercial usage of salt-effect distillation includes adding magnesium nitrate to an aqueous solution of nitric acid to concentrate it further. Calcium chloride is added to acetone-methanol and water-isopropanol mixtures in order to facilitate separation. [2]
References[edit]
- ^ Smallwood, Ian McN. (2002), Solvent Recovery Handbook (Second ed.), CRC Press, pp. 166–167, ISBN 0-8493-1602-2, retrieved 2007-11-30
- ^ "Salt-effect distillation", McGraw-Hill Dictionary of Scientific and Technical Terms, McGraw-Hill, 2003, retrieved 2007-11-30
See also[edit]
https://en.wikipedia.org/wiki/Salt-effect_distillation
Dry distillation is the heating of solid materials to produce gaseous products (which may condense into liquids or solids). The method may involve pyrolysis or thermolysis, or it may not (for instance, a simple mixture of ice and glass could be separated without breaking any chemical bonds, but organic matter contains a greater diversity of molecules, some of which are likely to break).
If there are no chemical changes, just phase changes, it resembles classical distillation, although it will generally need higher temperatures. Dry distillation in which chemical changes occur is a type of destructive distillation or cracking.
Uses[edit]
The method has been used to obtain liquid fuels from coal and wood. It can also be used to break down mineral salts such as sulfates (SO2−
4) through thermolysis, in this case producing sulfur dioxide (SO2) or sulfur trioxide (SO3) gas which can be dissolved in water to obtain sulfuric acid. By this method sulfuric acid was first identified and artificially produced. When substances of vegetable origin, e.g. coal, oil shale, peat or wood, are heated in the absence of air (dry distillation), they decompose into gas, liquid products and coke/charcoal. The yield and chemical nature of the decomposition products depend on the nature of the raw material and the conditions under which the dry distillation is done. Decomposition within a temperature range of 450 to about 600°C is called carbonization or low-temperature degassing. At temperatures above 900°C, the process is called coking or high-temperature degassing.[2] If coal is gasified to make coal gas or carbonized to make coke then Coal tar is among the by-products.
Wood[edit]
When wood is heated above 270°C it begins to carbonize. If air is absent, the final product (since there is no oxygen present to react with the wood) is charcoal. If air (which contains oxygen) is present, the wood will catch fire and burn when it reaches a temperature of about 400–500°C and the fuel product is wood ash. If wood is heated away from air, first the moisture is driven off. Until this is complete, the wood temperature remains at about 100–110°C. When the wood is dry its temperature rises, and at about 270°C, it begins to spontaneously decompose. This is the well known exothermic reaction which takes place in charcoal burning. At this stage evolution of the by-products of wood carbonization starts. These substances are given off gradually as the temperature rises and at about 450°C the evolution is complete. The solid residue, charcoal, is mainly carbon (about 70%) and small amounts of tarry substances which can be driven off or decomposed completely only by raising the temperature to above about 600°C.
In the common practice of charcoal burning using internal heating of the charged wood by burning a part of it, all the by-product vapors and gas escapes into the atmosphere as smoke. The by-products can be recovered by passing the off-gases through a series of water to yield so-called wood vinegar (pyroligneous acid) and the non-condensible wood gas passes on through the condenser and may be burned to provide heat. The wood gas is only usable as fuel and consists typically of 17% methane; 2% hydrogen; 23% carbon monoxide; 38% carbon dioxide; 2% oxygen and 18% nitrogen. It has a gas calorific value of about 10.8 MJ/m3 (290 BTU/cu.ft.) i.e. about one third the value of natural gas.[3] When deciduous tree woods are subjected to distillation, the products are methanol (wood alcohol) and charcoal. The distillation of pine wood causes Pine tar and pitch to drip away from the wood and leave behind charcoal. Birch tar from birch bark is a particularly fine tar, known as "Russian oil", suitable for leather protection. The by-products of wood tar are turpentine and charcoal.
Tar kilns are dry distillation ovens, historically used in Scandinavia for producing tar from wood. They were built close to the forest, from limestone or from more primitive holes in the ground. The bottom is sloped into an outlet hole to allow the tar to pour out. The wood is split into dimensions of a finger, stacked densely, and finally covered tight with dirt and moss. If oxygen can enter, the wood might catch fire, and the production would be ruined. On top of this, a fire is stacked and lit. After a few hours, the tar starts to pour out and continues to do so for a few days.
See also[edit]
https://en.wikipedia.org/wiki/Dry_distillation
Vacuum distillation is distillation performed under reduced pressure, which allows the purification of compounds not readily distilled at ambient pressures or simply to save time or energy. This technique separates compounds based on differences in their boiling points. This technique is used when the boiling point of the desired compound is difficult to achieve or will cause the compound to decompose.[1] Reduced pressures decrease the boiling point of compounds. The reduction in boiling point can be calculated using a temperature-pressure nomograph using the Clausius–Clapeyron relation.[2]
Laboratory-scale applications[edit]
Compounds with a boiling point lower than 150 °C typically are distilled at ambient pressure. For samples with high boiling points, short-path distillation apparatus is commonly employed.[3][4] This technique is amply illustrated in Organic Synthesis.[5] [6]
Rotary evaporation[edit]
Rotary evaporation[7] is a common technique used in laboratories to concentrate or isolate a compound from solution. Many solvents are volatile and can easily be evaporated using rotary evaporation. Even less volatile solvents can be removed by rotary evaporation under high vacuum and with heating. It is also used by environmental regulatory agencies for determining the amount of solvents in paints, coatings and inks.[8]
Safety considerations[edit]
Safety is an important consideration when glassware is under vacuum pressure. Scratches and cracks can result in implosions when the vacuum is applied. Wrapping as much of the glassware with tape as is practical helps to prevent dangerous scattering of glass shards in the event of an implosion.
Industrial-scale applications[edit]
Industrial-scale vacuum distillation[10] has several advantages. Close boiling mixtures may require many equilibrium stages to separate the key components. One tool to reduce the number of stages needed is to utilize vacuum distillation.[11] Vacuum distillation columns (as depicted in Figures 2 and 3) typically used in oil refineries have diameters ranging up to about 14 meters (46 feet), heights ranging up to about 50 meters (164 feet), and feed rates ranging up to about 25,400 cubic meters per day (160,000 barrels per day).
Vacuum distillation can improve a separation by:
- Prevention of product degradation or polymer formation because of reduced pressure leading to lower tower bottoms temperatures,
- Reduction of product degradation or polymer formation because of reduced mean residence time especially in columns using packing rather than trays.
- Increasing capacity, yield, and purity.
Another advantage of vacuum distillation is the reduced capital cost, at the expense of slightly more operating cost. Utilizing vacuum distillation can reduce the height and diameter, and thus the capital cost of a distillation column.
Vacuum distillation in petroleum refining[edit]
Petroleum crude oil is a complex mixture of hundreds of different hydrocarbon compounds generally having from 3 to 60 carbon atomsper molecule, although there may be small amounts of hydrocarbons outside that range.[12][13][14] The refining of crude oil begins with distilling the incoming crude oil in a so-called atmospheric distillation column operating at pressures slightly above atmospheric pressure.[10][12][13]
Vacuum distillation can also be referred to as "low-temperature distillation".
In distilling the crude oil, it is important not to subject the crude oil to temperatures above 370 to 380 °C because high molecular weightcomponents in the crude oil will undergo thermal cracking and form petroleum coke at temperatures above that. Formation of coke would result in plugging the tubes in the furnace that heats the feed stream to the crude oil distillation column. Plugging would also occur in the piping from the furnace to the distillation column as well as in the column itself.
The constraint imposed by limiting the column inlet crude oil to a temperature of less than 370 to 380 °C yields a residual oil from the bottom of the atmospheric distillation column consisting entirely of hydrocarbons that boil above 370 to 380 °C.
To further distill the residual oil from the atmospheric distillation column, the distillation must be performed at absolute pressures as low as 10 to 40 mmHg / Torr (About 5% atmospheric pressure) so as to limit the operating temperature to less than 370 to 380 °C.
Figure 2 is a simplified process diagram of a petroleum refinery vacuum distillation column that depicts the internals of the column and Figure 3 is a photograph of a large vacuum distillation column in a petroleum refinery.
The 10 to 40 mmHg absolute pressure in a vacuum distillation column increases the volume of vapor formed per volume of liquid distilled. The result is that such columns have very large diameters.[15]
Distillation columns such those in Images 1 and 2, may have diameters of 15 meters or more, heights ranging up to about 50 meters, and feed rates ranging up to about 25,400 cubic meters per day (160,000 barrels per day).
The vacuum distillation column internals must provide good vapor–liquid contacting while, at the same time, maintaining a very low-pressure increase from the top of the column top to the bottom. Therefore, the vacuum column uses distillation trays only where products are withdrawn from the side of the column (referred to as side draws). Most of the column uses packing material for the vapor–liquid contacting because such packing has a lower pressure drop than distillation trays. This packing material can be either structured sheet metal or randomly dumped packing such as Raschig rings.
The absolute pressure of 10 to 40 mmHg in the vacuum column is most often achieved by using multiple stages of steam jet ejectors.[16]
Many industries, other than the petroleum refining industry, use vacuum distillation on a much smaller scale. Copenhagen-based Empirical Spirits,[17] a distillery founded by former Noma chefs,[18] uses the process to create uniquely flavoured spirits. Their flagship spirit, Helena, is created using Koji, alongside Pilsner Malt and Belgian Saison Yeast.[19]
Large-scale water purification[edit]
Vacuum distillation is often used in large industrial plants as an efficient way to remove salt from ocean water, in order to produce fresh water. This is known as desalination. The ocean water is placed under a vacuum to lower its boiling point and has a heat source applied, allowing the fresh water to boil off and be condensed. The condensing of the water vapor prevents the water vapor from filling the vacuum chamber, and allows the effect to run continuously without a loss of vacuum pressure. The heat from condensation of the water vapor is removed by a heat sink, which uses the incoming ocean water as the coolant and thus preheats the feed of ocean water. Some forms of distillation do not use condensers, but instead compress the vapor mechanically with a pump. This acts as a heat pump, concentrating the heat from the vapor and allowing for the heat to be returned and reused by the incoming untreated water source. There are several forms of vacuum distillation of water, with the most common being multiple-effect distillation, vapor-compression desalination, and multi-stage flash distillation.[20]
Molecular distillation[edit]
Molecular distillation is vacuum distillation below the pressure of 0.01 torr[21] (1.3 Pa). 0.01 torr is one order of magnitude above high vacuum, where fluids are in the free molecular flow regime, i.e. the mean free path of molecules is comparable to the size of the equipment.[22] The gaseous phase no longer exerts significant pressure on the substance to be evaporated, and consequently, the rate of evaporation no longer depends on pressure. That is, because the continuum assumptions of fluid dynamics no longer apply, mass transport is governed by molecular dynamics rather than fluid dynamics. Thus, a short path between the hot surface and the cold surface is necessary, typically by suspending a hot plate covered with a film of feed next to a cold plate with a line of sight in between.
Molecular distillation is used industrially for purification of oils.[20]
Gallery[edit]
See also[edit]
https://en.wikipedia.org/wiki/Vacuum_distillation
Spinning cone columns are used in a form of low temperature vacuum steam distillation to gently extract volatile chemicals from liquid foodstuffs while minimising the effect on the taste of the product. For instance, the columns can be used to remove some of the alcohol from wine, 'off' smells from cream, and to capture aroma compounds that would otherwise be lost in coffee processing.
Mechanism[edit]
The columns are made of stainless steel. Conical vanes are attached alternately to the wall of the column and to a central rotating shaft. The product is poured in at the top under vacuum, and steam is pumped into the column from below.[1] The vanes provide a large surface area over which volatile compounds can evaporate into the steam, and the rotation ensures a thin layer of the product is constantly moved over the moving cone. It typically takes 20 seconds for the liquid to move through the column, and industrial columns might process 16–160 litres per minute (960–9,600 l/h; 4.2–42.3 US gal/min; 250–2,540 US gal/h). The temperature and pressure can be adjusted depending on the compounds targeted.
Wine controversy[edit]
Improvements in viticulture and warmer vintages have led to increasing levels of sugar in wine grapes, which have translated to higher levels of alcohol - which can reach over 15% ABV in Zinfandels from California. Some producers feel that this unbalances their wine, and use spinning cones to reduce the alcohol by 1-2 percentage points. In this case the wine is passed through the column once to distill out the most volatile aroma compounds which are then put to one side while the wine goes through the column a second time at higher temperature to extract alcohol. The aroma compounds are then mixed back into the wine. Some producers such as Joel Peterson of Ravenswood argue that technological "fixes" such as spinning cones remove a sense of terroir from the wine; if the wine has the tannins and other components to balance 15% alcohol, Peterson argues that it should be accepted on its own terms.[2]
The use of spinning cones, and other technologies such as reverse osmosis, was banned in the EU until recently, although for many years they could freely be used in wines imported into the EU from certain New World wine producing countries such as Australia and the USA.[3] In November 2007, the Wine Standards Branch (WSB) of the UK's Food Standards Agency banned the sale of a wine called Sovio,[3] made from Spanish grapes that would normally produce wines of 14% ABV.[4] Sovio runs 40-50% of the wine over spinning cones to reduce the alcohol content to 8%, which means that under EU law it could not be sold as wine as it was below 8.5%; above that, under the rules prevailing at the time, it would be banned because spinning cones could not be used in EU winemaking.[4]
Subsequently, the EU legalized dealcoholization with a 2% adjustment limit in its Code of Winemaking Practices, publishing that in its Commission Regulation (EC) No 606/2009[5] and stipulating that the dealcoholization must be accomplished by physical separation techniques which would embrace the spinning cone method.
More recently, in International Organisation of Vine and Wine Resolutions OIV-OENO 394A-2012[6] and OIV-OENO 394B-2012[7] of June 22, 2012 EU recommended winemaking procedures were modified to permit use of the spinning cone column and membrane techniques such as reverse osmosis on wine, subject to a 20% limitation on the adjustment. That limitation is currently under review following the proposal by some EU members that it be eliminated altogether. The limitation is applicable only to products formally labeled as "wine".
See also[edit]
https://en.wikipedia.org/wiki/Spinning_cone
Spinning band distillation is a technique used to separate liquid mixtures which are similar in boiling points. When liquids with similar boiling points are distilled, the vapors are mixtures, and not pure compounds. Fractionating columns help separate the mixture by allowing the mixed vapors to cool, condense, and vaporize again in accordance with Raoult's law. With each condensation-vaporization cycles, the vapors are enriched in a certain component. A larger surface area allows more cycles, improving separation.
Spinning band distillation takes this concept one step further by using a spinning helical band made of an inert material such as metal or Teflon to push the rising vapors and descending condensate to the sides of the column, coming into close contact with each other. This speeds up equilibration and provides for a greater number of condensation-vaporization cycles.
Applications[edit]
Spinning band distillation may sometimes be used to recycle waste solvents which contain different solvents, and other chemical compounds.[citation needed]
See also[edit]
- Spinning cone
- The French Wikipedia webpage for Spinning Band Distillation contains more information than the English language version (here) and a few images that are missing from this webpage.
References[edit]
- B/R Instrument Corporation, Spinning Band Distillation, accessed 27 Oct, 2006.
- B/R Instrument Corporation, Comparison of Spinning Band Distillation with Packed Column Distillation, accessed 27 Oct 2006.
- Marshall Space Flight Center, Two Methods for Purifying Carbon Tetrachloride. Accessed 27 Oct 2006.
References[edit]
- ^ Price, Overton W.; Kellogg, R.S.; Cox, W.T. (1909). Forests of the United States: Their Use. Government printing office.
- ^ Eagleson, Mary (1994). Concise Encyclopedia Chemistry. Walter de Gruyter. pp. 240–. ISBN 978-3-11-011451-5.
- ^ "Volume 41 of FAO forestry paper". Simple Technologies for Charcoal Making, Issue 41 of Forestry Papers Series. Food & Agriculture Org. 1983. ISBN 9251013284. Retrieved 15 February 2015.
Tar is a dark brown or black viscous liquid of hydrocarbons and free carbon, obtained from a wide variety of organic materialsthrough destructive distillation. Tar can be produced from coal, wood, petroleum, or peat.[1]
Mineral products resembling tar can be produced from fossil hydrocarbons, such as petroleum. Coal tar is produced from coal as a byproduct of coke production.
https://en.wikipedia.org/wiki/Tar
In petrochemistry, petroleum geology and organic chemistry, cracking is the process whereby complex organic molecules such as kerogens or long-chain hydrocarbons are broken down into simpler molecules such as light hydrocarbons, by the breaking of carbon-carbon bonds in the precursors. The rate of cracking and the end products are strongly dependent on the temperature and presence of catalysts. Cracking is the breakdown of a large alkane into smaller, more useful alkenes. Simply put, hydrocarbon cracking is the process of breaking a long chain of hydrocarbons into short ones. This process requires high temperatures.[1]
More loosely, outside the field of petroleum chemistry, the term "cracking" is used to describe any type of splitting of molecules under the influence of heat, catalysts and solvents, such as in processes of destructive distillation or pyrolysis.
Fluid catalytic cracking produces a high yield of petrol and LPG, while hydrocracking is a major source of jet fuel, diesel fuel, naphtha, and again yields LPG.
https://en.wikipedia.org/wiki/Cracking_(chemistry)
The pyrolysis (or devolatilization) process is the thermal decomposition of materials at elevated temperatures in an inert atmosphere.[1] It involves a change of chemical composition. The word is coined from the Greek-derived elements pyro "fire", "heat", "fever" and lysis "separating".
Pyrolysis is most commonly used in the treatment of organic materials. It is one of the processes involved in charring wood.[2]In general, pyrolysis of organic substances produces volatile products and leaves char, a carbon-rich solid residue. Extreme pyrolysis, which leaves mostly carbon as the residue, is called carbonization. Pyrolysis is considered the first step in the processes of gasification or combustion.[3][4]
The process is used heavily in the chemical industry, for example, to produce ethylene, many forms of carbon, and other chemicals from petroleum, coal, and even wood, to produce coke from coal. It is used also in the conversion of natural gas(primarily methane) into hydrogen gas and solid carbon char, recently on an industrial scale.[5] Aspirational applications of pyrolysis would convert biomass into syngas and biochar, waste plastics back into usable oil, or waste into safely disposable substances.
https://en.wikipedia.org/wiki/Pyrolysis
Turpentine (which is also called spirit of turpentine, oil of turpentine, terebenthene, terebinthine and (colloquially) turps)[2] is a fluid obtained by the distillation of resin harvested from living trees, mainly pines. Mainly used as a specialized solvent, it is also a source of material for organic syntheses.
Turpentine is composed of terpenes, primarily the monoterpenes alpha- and beta-pinene, with lesser amounts of carene, camphene, dipentene, and terpinolene.[3] Mineral turpentine or other petroleum distillates are used to replace turpentine – although the constituent chemicals are very different.[4]
https://en.wikipedia.org/wiki/Turpentine
White spirit (UK & Ireland)[note 1] or mineral spirits (US, Canada), also known as mineral turpentine (AU/NZ), turpentine substitute, and petroleum spirits, is a petroleum-derived clear liquid used as a common organic solvent in painting.[1] There are also terms for specific kinds of mineral spirits, including Stoddard solvent and solvent naphtha (petroleum). Mineral spirits are often used as a paint thinner, or as a component thereof, though paint thinner is a broader category of solvent. Odorless mineral spirits (OMS) have been refined to remove the more toxic aromatic compounds, and are recommended for applications such as oil painting.
A mixture of aliphatic, open-chain or alicyclic C7 to C12 hydrocarbons, white spirit is insoluble in water and is used as an extraction solvent, as a cleaning solvent, as a degreasing solvent and as a solvent in aerosols, paints, wood preservatives, lacquers, varnishes, and asphalt products. In western Europe about 60% of the total white spirit consumption is used in paints, lacquers and varnishes.[1] White spirit is the most widely used solvent in the paint industry. In households, white spirit is commonly used to clean paint brushes after use, to clean auto parts and tools, as a starter fluid for charcoal grills, to remove adhesive residue from non-porous surfaces, and many other common tasks.
The word "mineral" in "mineral spirits" or "mineral turpentine" is meant to distinguish it from distilled spirits (distilled directly from fermented grains and fruit) or from true turpentine (distilled tree resin).
https://en.wikipedia.org/wiki/White_spirit
Petroleum, also known as crude oil, or simply oil, is a naturally occurring yellowish-black liquid mixture of mainly hydrocarbons,[1] and is found in geological formations. The name petroleum covers both naturally occurring unprocessed crude oil and petroleum products that consist of refined crude oil. A fossil fuel, petroleum is formed when large quantities of dead organisms, mostly zooplankton and algae, are buried underneath sedimentary rock and subjected to both prolonged heat and pressure.
https://en.wikipedia.org/wiki/Petroleum
Paraquat (trivial name; /ˈpærəkwɒt/), or N,N′-dimethyl-4,4′-bipyridinium dichloride (systematic name), also known as methyl viologen, is an organic compound with the chemical formula [(C6H7N)2]Cl2. It is classified as a viologen, a family of redox-active heterocycles of similar structure.[5] This salt is one of the most widely used herbicides. It is quick-acting and non-selective, killing green plant tissue on contact. It is also toxic (lethal) to human beings and animals due to its redox activity, which produces superoxide anions. It has been linked to the development of Parkinson's disease[6][7] and is banned in several countries.
Paraquat may be in the form of salt with chloride or other anions; quantities of the substance are sometimes expressed by cation mass alone (paraquat cation, paraquat ion).
The name is derived from the para positions of the quaternary nitrogens.
https://en.wikipedia.org/wiki/Paraquat
Charcoal is a lightweight black carbon residue produced by strongly heating wood (or other animal and plant materials) in minimal oxygen to remove all water and volatile constituents. In the traditional version of this pyrolysis process, called charcoal burning, often by forming a charcoal kiln, the heat is supplied by burning part of the starting material itself, with a limited supply of oxygen. The material can also be heated in a closed retort. Modern "charcoal" briquettes used for outdoor cooking may contain many other additives, e.g. coal.
This process happens naturally when combustion is incomplete, and is sometimes used in radiocarbon dating. It also happens inadvertently while burning wood, as in a fireplace or wood stove. The visible flame in these is due to combustion of the volatile gases exuded as the wood turns into charcoal. The soot and smoke commonly given off by wood fires result from incomplete combustion of those volatiles. Charcoal burns at a higher temperature than wood, with hardly a visible flame, and releases almost nothing except heat and carbon dioxide (One kilogram of charcoal contains 680 to 820 grams of carbon, which when combined with oxygen from the atmosphere form 2.5 to 3 kg of carbon dioxide).
https://en.wikipedia.org/wiki/Charcoal
Pyroligneous acid, also called wood vinegar or wood acid,[3] is a dark liquid produced by the destructive distillation of wood and other plant materials.[1]
https://en.wikipedia.org/wiki/Pyroligneous_acid
References[edit]
- ^ Pyroligneous acid from Sigma-Aldrich
- ^ George A. Burdock (2010), "PYROLIGNEOUS ACID", Fenaroli's Handbook of Flavor Ingredients (6th ed.), Taylor & Francis, pp. 1774–1775, ISBN 978-1-4200-9077-2
- ^ Webster's Revised Unabridged Dictionary (1913)
- ^ Fielding H. Garrison (1921), History of Medicine (3rd ed.), W. B. Saunders, p. 286
- ^ Johann Rudolph Glauber (1651), Furni Novi Philosophici, vol. 1, Johann Jansson, pp. 47–49
- ^ Mark Kurlansky (2002). Salt: A World History. Penguin Books. pp. 267–68. ISBN 0-14-200161-9.
- ^ Ganswindt, Albert (1889). Handbuch der Färberei und der damit verwandten vorbereitenden und vollendenden Gewerbe (in German). p. 270.
- ^ Unusual Stories of Unusual Men: Ernest H. Wright - Classification: "Condensed Smoke". The Rotarian. 1923. pp. 209–10, 240.
- ^ Bruce Kraig (31 January 2013). The Oxford Encyclopedia of Food and Drink in America. OUP USA. pp. 2–. ISBN 978-0-19-973496-2.
https://en.wikipedia.org/wiki/Pyroligneous_acid
No comments:
Post a Comment