A phonograph disc record (also known as a gramophone disc record, especially in British English), or simply a phonograph record, gramophone record, disc record or record, is an analog sound storage medium in the form of a flat disc with an inscribed, modulated spiral groove. The groove usually starts near the periphery and ends near the center of the disc. At first, the discs were commonly made from shellac, with earlier records having a fine abrasive filler mixed in. Starting in the 1940s polyvinyl chloride became common, hence the name "vinyl". In the mid-2000s, gradually, records made of any material began to be called vinyl disc records, also known as vinyl records or vinyl for short.
The phonograph disc record was the primary medium used for music reproduction throughout the 20th century. It had co-existed with the phonograph cylinder from the late 1880s and had effectively superseded it by around 1912. Records retained the largest market share even when new formats such as the compact cassette were mass-marketed. By the 1980s, digital media, in the form of the compact disc, had gained a larger market share, and the record left the mainstream in 1991.[1] Since the 1990s, records continue to be manufactured and sold on a smaller scale, and during the 1990s and early 2000s were commonly used by disc jockeys (DJs), especially in dance music genres. They were also listened to by a growing number of audiophiles. The phonograph record has made a niche resurgence as a format for rock music in the early 21st century—9.2 million records were sold in the US in 2014, a 260% increase since 2009.[2] Likewise, sales in the UK increased five-fold from 2009 to 2014.[3]
As of 2017, 48 record pressing facilities remain worldwide, 18 in the US and 30 in other countries. The increased popularity of the record has led to the investment in new and modern record-pressing machines.[4] Only two producers of lacquers (acetate discs or master discs) remain: Apollo Masters in California, and MDC in Japan.[5] On February 6, 2020, a fire destroyed the Apollo Masters plant. According to the Apollo Masters website, their future is still uncertain.[6]
Phonograph records are generally described by their diameter in inches (12-inch, 10-inch, 7-inch) (although they were designed in millimeters[7]), the rotational speed in revolutions per minute (rpm) at which they are played (81⁄3, 162⁄3, 331⁄3, 45, 78),[8] and their time capacity, determined by their diameter and speed (LP [long playing], 12-inch disc, 331⁄3 rpm; SP [single], 10-inch disc, 78 rpm, or 7-inch disc, 45 rpm; EP [extended play], 12-inch disc or 7-inch disc, 331⁄3 or 45 rpm); their reproductive quality, or level of fidelity (high-fidelity, orthophonic, full-range, etc.); and the number of audio channels (mono, stereo, quad, etc.).
The phrase broken record refers to a malfunction[9] when the needle skips/jumps back to the previous groove and plays the same section over and over again indefinitely.[10][11][12]
The large cover (and inner sleeves) are valued by collectors and artists for the space given for visual expression, especially in the case of 12-inch discs.[citation needed]
https://en.wikipedia.org/wiki/Phonograph_record
Phonograph cylinders are the earliest commercial medium for recording and reproducing sound. Commonly known simply as "records" in their era of greatest popularity (c. 1896–1915), these hollow cylindrical objects have an audio recording engraved on the outside surface, which can be reproduced when they are played on a mechanical cylinder phonograph.[1] In the 1910s, the competing disc record system triumphed in the marketplace to become the dominant commercial audio medium.[2]
https://en.wikipedia.org/wiki/Phonograph_cylinder
Celluloids are a class of materials produced by mixing nitrocellulose and camphor, often with added dyes and other agents. Once much more common for its use as photographic film before the advent of safer methods, celluloid's common contemporary uses are table tennis balls, musical instruments, combs, office equipment, and guitar picks.[1][2]
History[edit]
Celluloid originated in 1856, when Alexander Parkes created Parkesine, generally considered the first thermoplastic.[3] In 1869, Daniel Spill, who had taken over Parkes' firm, renamed Parkesine as Xylonite. In the same year, John Wesley Hyatt patented it at the US Patent Office as Celluloid. Celluloid was easily molded and shaped, and it was first widely used as an ivory replacement.
The main use was in movie and photography film industries, which used only celluloid film stock prior to the adoption of acetate safety film in the 1950s. Celluloid is highly flammable, difficult and expensive to produce and no longer widely used.
Nitrocellulose[edit]
Nitrocellulose-based plastics slightly predate celluloid. Collodion, invented in 1848 and used as a wound dressing and an emulsion for photographic plates, is dried to a celluloid like film.
Alexander Parkes[edit]
The first celluloid as a bulk material for forming objects was made in 1855 in Birmingham, England, by Alexander Parkes, who was never able to see his invention reach full fruition, after his firm went bankrupt due to scale-up costs.[4] Parkes patented his discovery as Parkesine in 1862 after realising a solid residue remained after evaporation of the solvent from photographic collodion.[5]
Parkes patented it as a clothing waterproofer for woven fabrics in the same year. Later Parkes showcased Parkesine at the 1862 International Exhibition in London, where he was awarded a bronze medal for his efforts. The introduction of Parkesine is generally regarded as the birth of the plastics industry.[4] Parkesine was made from cellulose treated with nitric acid and a solvent. It is often called synthetic ivory. The Parkesine company ceased trading in 1868. Pictures of Parkesine are held by the Plastics Historical Society of London. There is a plaque on the wall of the site of the Parkesine Works in Hackney, London.[6]
John Wesley Hyatt[edit]
In the 1860s, an American, John Wesley Hyatt, acquired Parkes's patent and began experimenting with cellulose nitrate with the intention of manufacturing billiard balls, which until that time were made from ivory. He used cloth, ivory dust, and shellac, and on April 6, 1869, patented a method of covering billiard balls with the addition of collodion. With assistance from Peter Kinnear and other investors,[7] Hyatt formed the Albany Billiard Ball Company (1868–1986) in Albany, New York, to manufacture the product. In 1870, John and his brother Isaiah patented a process of making a "horn-like material" with the inclusion of cellulose nitrate and camphor.[8] Alexander Parkes and Daniel Spill (see below) listed camphor during their earlier experiments, calling the resultant mix "xylonite", but it was the Hyatt brothers who recognized the value of camphor and its use as a plasticizer for cellulose nitrate. Isaiah Hyatt dubbed his material "celluloid" in 1872.
Daniel Spill and legal disputes[edit]
English inventor Daniel Spill had worked with Parkes and formed the Xylonite Co. to take over Parkes' patents, describing the new plastic products as Xylonite. He took exception to the Hyatts' claims and pursued the brothers in a number of court cases between 1877 and 1884. Initially the judge found in Spill's favour, but ultimately it was judged that neither party held an exclusive claim and the true inventor of celluloid/xylonite was Alexander Parkes, due to his mention of camphor in his earlier experiments and patents.[9] The judge ruled all manufacturing of celluloid could continue both in Spill's British Xylonite Company and Hyatts' Celluloid Manufacturing Company.
The name Celluloid actually began as a trademark of the Celluloid Manufacturing Company, first of Albany, NY, and later of Newark, New Jersey, which manufactured the celluloids patented by John Wesley Hyatt. Hyatt used heat and pressure to simplify the manufacture of these compounds. Over the years, celluloid became the common use term used for this type of plastic. In 1878 Hyatt was able to patent a process for injection moulding thermoplastics, although it took another fifty years before it could be realised commercially, and in later years celluloid was used as the base for photographic film.[10]
Photography[edit]
English photographer John Carbutt founded the Keystone Dry Plate Works in 1879 with the intention of producing gelatin dry plates.[11] The Celluloid Manufacturing Company was contracted for this work, which was done by thinly slicing layers out of celluloid blocks and then removing the slice marks with heated pressure plates. After this, the celluloid strips were coated with a photosensitive gelatin emulsion. It is not certain exactly how long it took for Carbutt to standardize his process, but it occurred no later than 1888. A 15-inch-wide (380 mm) sheet of Carbutt's film was used by William Dicksonfor the early Edison motion picture experiments on a cylinder drum Kinetograph. However, the celluloid film base produced by this means was still considered too stiff for the needs of motion-picture photography.
By 1889, more flexible celluloids for photographic film were developed, and both Hannibal Goodwin and the Eastman Kodak Company obtained patents for a film product. (Ansco, which purchased Goodwin's patent after he died, was eventually successful in a patent-infringement suit against Kodak). This ability to produce photographic images on a flexible material (as opposed to a glass or metal plate) was a crucial step toward making possible the advent of motion pictures.
Uses[edit]
Most movie and photography films prior to the widespread move to acetate films in the 1950s were made of celluloid. Its high flammability was legendary since it self-explodes when exposed to temperatures over 150° C in front of a hot movie-projector beam. While celluloid film was standard for 35mm theatrical productions until around 1950, motion-picture film for amateur use, such as 16mm and 8mm film, were on acetate "safety base", at least in the US.
Celluloid is useful for producing cheaper jewellery, jewellery boxes, hair accessories and many items that would earlier have been manufactured from ivory, horn or other expensive animal products.[1] It was often referred to as "Ivorine" or "French Ivory". For this use, a form of celluloid was developed in France that had lines in it to make it resemble ivory.[12] It was also used for dressing table sets, dolls, picture frames, charms, hat pins, buttons, buckles, stringed instrument parts, accordions, fountain pens, cutlery handles and kitchen items. The main disadvantage the material had was that it was flammable. It was soon overtaken by Bakelite and Catalin. Table tennis balls were made from celluloid until 2014. "Parker Brothers... made some versions [of diabolos] out of hollow Celluloid--which, because of its 'frictionless' properties, spun even faster than steel."[13]
Shelf clocks and other furniture items were often covered with celluloid in a manner similar to veneer. This celluloid was printed to look like expensive woods, or materials like marble or granite. The Seth Thomas clock company called its celluloid clock material "adamantine". Celluloid enabled clockmakers to make the typical late Victorian style of black mantel clock in such a way that the wooden case appeared to be black marble, and the various pillars and other decorative elements of the case looked like semi-precious stone.[14]
Celluloid was also a popular material in the construction of slide rules. It was primarily used to coat wooden slide rule faces, such as in early A.W. Faber rules, as well as cursor end pieces, such as in Keuffel and Esser rules.
Celluloid remains in use for musical instruments, especially accordions and guitars. Celluloid is very robust and easy to mold in difficult forms, and has great acoustic performance as cover for wooden frames since it does not block wood's natural pores. Instruments covered with celluloid can easily be recognized by the material's typical nacre-like flaming pattern. Thick celluloid panels are cooked in a bain-marie which turns them into a leather-like substance. Panels are then turned on a mold and allowed to harden for as long as three months.
Formulation[edit]
A typical formulation of celluloid might contain 70 to 80 parts nitrocellulose, nitrated to 11% nitrogen, 30 parts camphor, 0 to 14 parts dye, 1 to 5 parts ethyl alcohol, plus stabilizers and other agents to increase stability and reduce flammability.
Production[edit]
Celluloid is made from a mixture of chemicals such as nitrocellulose, camphor, alcohol, as well as colorants and fillers depending on the desired product. The first step is transforming raw cellulose into nitrocellulose by conducting a nitration reaction. This is achieved by exposing the cellulose fibers to an aqueous solution of nitric acid; the hydroxyl groups (-OH) will then be replaced with nitrate groups (-ONO2) on the cellulose chain. The reaction can produce mixed products, depending on the degree of substitution of nitrogen, or the percent nitrogen content on each cellulose molecule; cellulose nitrate has 2.8 molecule of nitrogen per molecule of cellulose. It was determined that sulfuric acid was to be used as well in the reaction in order to first, catalyze the nitric acid groups so it can allow for the substitution onto the cellulose, and second, allow for the groups to easily and uniformly attach to the fibers, creating a better quality nitrocellulose. The product then must be rinsed to wash away any free acids that did not react with the fibers, dried, and kneaded. During this time, a solution of 50% camphor in alcohol is added, which then changes the macromolecule structure of nitrocellulose into a homogeneous gel of nitrocellulose and camphor. The chemical structure is not well understood, but it is determined that it is one molecule of camphor for each unit of glucose. After the mixing, the mass is pressed into blocks at a high pressure and then is fabricated for its specific use.[15]
Nitrating cellulose is an extremely flammable process in which even factory explosions are not uncommon. Many western celluloid factories closed after hazardous explosions, and only two factories in China remain in business.
Environmental hazards[edit]
Deterioration[edit]
Many sources of deterioration in celluloid exist, such as thermal, chemical, photochemical, and physical. The most inherent flaw is as celluloid ages, the camphor molecules are ‘squeezed’ out of the mass due to the unsustainable pressure used in the production. That pressure causes the nitrocellulose molecules to bind back to each other or crystallize, and this results in the camphor molecules being shoved out of the material. Once exposed to the environment, camphor can undergo sublimation at room temperature, leaving the plastic as brittle nitrocellulose. Also, with exposure to excess heat, the nitrate groups can break off and expose nitrogen gases, such as nitrous oxide and nitric oxide,[16] to the air.
Another factor that can cause this is excess moisture, which can accelerate deterioration of nitrocellulose with the presence of nitrate groups, either newly fragmented from heat or still trapped as a free acid from production. Both of these sources allow the accumulation of nitric acid. Another form of deterioration, photochemical deterioration, is severe in celluloid because it absorbs ultraviolet light well. The absorbed light leads to chain-breakage and stiffening.[15]
Among collectors of antiques, the deterioration of celluloid is generally known as "celluloid rot." The chemical processes involved are not perfectly understood, but it is widely believed that the gases released by a piece undergoing celluloid rot can trigger celluloid rot in nearby articles of celluloid which were previously intact.[17]
See also[edit]
https://en.wikipedia.org/wiki/Celluloid
Subcategories
This category has the following 2 subcategories, out of 2 total.
Pages in category "Thermoplastics"
The following 82 pages are in this category, out of 82 total. This list may not reflect recent changes (learn more).
E
P
- Pearloid
- Perfluoroalkoxy alkane
- Perfluoroether
- PHBV
- Plastarch material
- Plastisol
- Poly(ethyl methacrylate)
- Poly(methyl methacrylate)
- Polyphenylene sulfide
- Polyacrylonitrile
- Polyamide
- Polyamide-imide
- Polyaryletherketone
- Polybutadiene
- Polybutylene succinate
- Polybutylene terephthalate
- Polycaprolactone
- Polycarbonate
- Polychlorotrifluoroethylene
- Polycyclohexylenedimethylene terephthalate
- Polyester
- Polyether ether ketone
- Polyetherimide
- Polyetherketoneketone
- Polyethylene
- Polyethylene terephthalate
- Polyglycolide
- Polyhydroxyalkanoates
- Polyhydroxybutyrate
- Polyimide
- Polyketone
- Polylactic acid
- Polymethylpentene
- Polyoxymethylene
- Polyphthalamide
- Polypropylene
- Polystyrene
- Polysulfone
- Polyvinyl chloride
- Polyvinyl ester
- Polyvinyl fluoride
- Polyvinylcarbazole
- Polyvinylidene chloride
- Polyvinylidene fluoride
- Pulverized Vinsol resin
- PVC clothing
Z
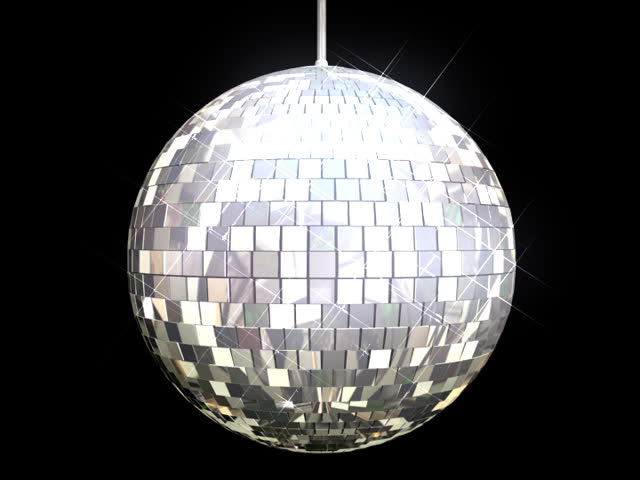
Liquid crystal polymers (LCPs) are polymers with the property of liquid crystal, usually containing aromatic rings as mesogens. Despite uncrosslinked LCPs, polymeric materials like LCEs (liquid crystal elastomers) and LCNs (liquid crystal networks) can exhibit liquid crystallinity as well. They are both crosslinked LCPs but have different cross link density.[1] They are already widely used in the display market.[2] In addition, LCPs have unique properties like thermal actuation, anisotropic swelling, and soft elasticity. Therefore, they can be good actuators and sensors.[3] One of the most famous and classical applications for LCPs is Kevlar, a strong but light fiber with wide applications like a bulletproof vest.
Background[edit]
Liquid crystallinity in polymers may occur either by dissolving a polymer in a solvent (lyotropic liquid-crystal polymers) or by heating a polymer above its glass or melting transition point (thermotropic liquid-crystal polymers).[5] Liquid-crystal polymers are present in melted/liquid or solid form.[6] In solid form the main example of lyotropic LCPs is the commercial aramid known as Kevlar. Chemical structure of this aramid consists of linearly substituted aromatic rings linked by amide groups. In a similar way, several series of thermotropic LCPs have been commercially produced by several companies (e.g., Vectra / Celanese).
A high number of LCPs, produced in the 1980s, displayed order in the melt phase analogous to that exhibited by nonpolymeric liquid crystals. Processing of LCPs from liquid-crystal phases (or mesophases) gives rise to fibers and injected materials having high mechanical properties as a consequence of the self-reinforcing properties derived from the macromolecular orientation in the mesophase.
Today, LCPs can be melt-processed on conventional equipment at high speeds with excellent replication of mold details. In fact, the high ease of forming of LCPs is an important competitive advantage against other plastics, as it offsets high raw material cost.[7]
The class of polar and bowlic LCPs, with unique properties and important potential applications, remains to be exploited.[8]
Mesophases[edit]
Same as the small molecular liquid crystal, liquid crystal polymers also have different mesophases. The mesogen cores of the polymers will aggregate into different mesophases: Nematics (N), Cholesterics (Ch), Smectics (S), compounds with highly plar end groups.[9] More information about the mesophases can be found on liquid crystal page.
Classification[edit]
LCPs are categorized by the location of liquid crystal cores. Main chain liquid crystal polymers (MCLCPs), as the name indicates, have liquid crystal cores in the main chain. To contrast, side chain liquid crystal polymers (SCLCPs) have pendant side chains containing the liquid crystal cores. The basic structures for these two kinds of LCPs are shown in the figure.[9]
Main chain LCP[edit]
Main chain LCPs have rigid, rod-like mesogens in the polymer backbones, which indirectly leads to the high melting temperature of this kind of LCPs. To make this kind of polymer easy to process, different methods are applied to lower the transition temperature: (1) Introducing flexible sequences; (2) Introducing bends or kinks; (3) Adding substituent groups to the aromatic mesogens...
Side Chain LCP[10][edit]
In side chain LCPs, the mesogens are in the polymer side chains. The mesogens usually are linked to the backbones through flexible spacers (Although for a few LCPs, the side chains directly link to the backbones). If the mesogens are directly linked to the backbones, the coil-like conformation of the backbones will impede the mesogens from forming an orientational structure. However, by introducing flexible spacers between the backbones and the mesogens, the ordering of mesogens can be decoupled from the conformation of the backbones.
Becasause of the researcher's effort, more and more LCPs of different structures are synthesized. Therefore, latin letters are used to help the classification of LCPs.[9]
Mechanism[edit]
Mesogens in LCPs can self-organize to form liquid crystal regions in different conditions. Based on the mechanism of aggregation and ordering, LCPs can be roughly divided into two subcategories as shown below. However, the distinction is not rigidly defined. LCPs can be transformed into liquid crystals with more than one method.[9]
Lyotropic systems[11][edit]
Lyotropic main chain LCPs have rigid mesogen cores (like aromatic rings) in the backbones. This kind of LCPs forms liquid crystals due to their rigid chain conformation but not only the aggregation of mesogen cores. Because of the rigid structure, strong solvent is needed to dissolve the lyotropic main chain polymers. When the concentration of the polymers reaches critical concentration, the mesophases begin to form and the viscosity of the polymer solution begins to decrease. Lyotropic main chain LCPs have been mainly used to generate high-strength fibers such as Kevlar.
Side chain LCPs usually consist of both hydrophobic and hydrophilic segments. Usually, the side chain ends are hydrophilic. When they are dissolved in water, micelles will form due to hydrophobic force. If the volume fraction of the polymers exceeds the critical volume fraction, the micellar segregates will be packed to form a liquid crystal structure. As the concentration varies above the critical volume fraction, the liquid crystal generated may have different packing ways. Temperature, the stiffness of the polymers, molecular weight of the polymers can affect the liquid crystal transformation. Lyotropic side chain LCPs like alkyl polyoxyethylene surfactants attached to polysiloxane polymers may be applied to personal care products like liquid soap etc.
Thermotropic systems[12][edit]
The study of thermotropic LCPs is inspired by the success of the lyotropic LCPs. This kind of LCPs can only be processable when the melting temperature is far below the decomposition temperature. Above the melting temperature and glass transition temperature and below the clearing point, the thermotropic LCPs will form liquid crystals. After the clearing point, the melt will be isotropic and clear again. What is different from the small molecular liquid crystals is that we can get frozen liquid crystals by quenching the liquid crystal polymers below the glass transition temperature. Moreover, we can use copolymerization to justify the melting temperature and mesophase temperature.
There are other systems like phototropic systems.
Liquid crystal elastomers (LCEs)[3][edit]
LCEs is first proposed in 1981 by Finkelmann. After that, LCEs have attracted a lot of attention from researches and industry. LCEs can be synthesized both from the polymeric precursors and from exclusively monomers. LCEs can show special properties when responding to heat, light, and magnetic fields.[1]Furthermore, Different nanomaterials can be introduced into the LCE matrix (LCE-based composites) to provide LCEs with different properties and tailor LCEs' ability to respond to different stimuli.[3] LCEs have many applications. For example, the LCE films can be used as optical retarders due to their anisotropic structure. Because they can control the polarization state of the transmitted light, they are commonly used in 3D glasses, patterned retarders for transflective displays, the flat panel LC television. If the LCE is modified with azobenzene, it can show light response properties and thus can be applied for controlled wettability, autonomous lenses, and haptic surfaces.[2] Besides the display application which has already been commoditized, now researches have focused on other interesting properties of the LCEs like its special thermally and photogenerated macroscale mechanical responses, which means they can be good actuators. A recent paper systematically reviewed the programmable and adaptive mechanics with liquid crystal polymer networks and elastomers.[1]
There are different synthetic routes to get LCEs.[3]
LCEs synthesized from the polymeric precursors[edit]
LCEs synthesized from the polymeric precursors can be divided into two subcategories:
LCEs can be synthesized from poly(hydrosiloxane). A two-step crosslinking technique is applied to get LCEs from poly(hydrosiloxane). Poly(dydrosiloxane) is mixed with a monovinyl-functionalized liquid crystalline monomer, a multifunctional vinyl crosslinker, and catalyst. This mixture is used to generate a weakly crosslinked gel, in which the monomers are linked to the poly(dydrosiloxane) backbones. During the first crosslinking step or shortly after that, orientation is introduced into the mesogen cores of the gel with mechanical alignment methods. After that, the gel is dehydrated and the crosslinking reaction is completed. Therefore, the orientation is kept in the elastomer by crosslinking. In this way, we can get highly ordered side chain LCEs, which are also called single-crystal or monodomain LCEs.
LCEs can be synthesized from LCPs. With LCPs as precursors, we can use the two-step method shown in the previous subcategory. Also, we can use aligned LCPs mixed with multifunctional crosslinkers to directly generate LCEs. The mixture is first heated to isotopic. Fibers are drawn from the mixture and then crosslinked, thus the orientation can be trapped in the LCE. This method is widely used to generate a lot of LCEs. However, it is limited by the difficulty of processing caused by the high viscosity of the starting material.
LCEs synthesized from low molar mass monomers[edit]
Liquid crystal low molar mass monomers are mixed with crosslinkers and catalysts. The monomers can be aligned and then polymerized to keep the orientation. One advantage of this method is that the low molar mass monomers can be aligned by not only mechanical alignment, but also diamagnetic, dielectric, surface alignment. In recent years, methods to get a well-defined structure in LCEs have attracted a lot of attention. For example, thiol-ene radical step-growth polymerization and Michael addition are used to get well-ordered LCEs.[13] This is also a good way to synthesize moderately to densely crosslinked glassy LCNs.
The main difference between LCEs and LCNs is the cross link density. LCNs are primarily synthesized from (meth)acrylate-based multifunctional monomers while LCEs usually come from crosslinked polysiloxanes. More information about the synthesis, properties and applications of LCNs and LCEs can be found in this book published in 2011.[14]
Properties[edit]
A unique class of partially crystalline aromatic polyesters based on p-hydroxybenzoic acid and related monomers, liquid-crystal polymers are capable of forming regions of highly ordered structure while in the liquid phase. However, the degree of order is somewhat less than that of a regular solid crystal. Typically, LCPs have a high mechanical strength at high temperatures, extreme chemical resistance, inherent flame retardancy, and good weatherability. Liquid-crystal polymers come in a variety of forms from sinterable high temperature to injection moldable compounds. LCPs can be welded, though the lines created by welding are a weak point in the resulting product. LCPs have a high Z-axis coefficient of thermal expansion.
LCPs are exceptionally inert. They resist stress cracking in the presence of most chemicals at elevated temperatures, including aromatic or halogenated hydrocarbons, strong acids, bases, ketones, and other aggressive industrial substances. Hydrolytic stability in boiling water is excellent. Environments that deteriorate the polymers are high-temperature steam, concentrated sulfuric acid, and boiling caustic materials.
Polar and bowlic LCPs are ferroelectrics, with reaction time order-of-magnitudes smaller than that in conventional LCs and could be used to make ultrafast switches. Bowlic columnar polymers possess long, hollow tubes; with metal or transition metal atoms added into the tube, they could potentially form ultrahigh-Tc superconductors.[15]
Uses[edit]
Because of their various properties, LCPs are useful for electrical[16] and mechanical parts, food containers, and any other applications requiring chemical inertness and high strength. LCP is particularly good for microwave frequency electronics due to low relative dielectric constants, low dissipation factors, and commercial availability of laminates. Packaging microelectromechanical systems (MEMS) is another area that LCP has recently gained more attention. The superior properties of LCPs make them especially suitable for automotive ignition system components, heater plug connectors, lamp sockets, transmission system components, pump components, coil forms and sunlight sensors and sensors for car safety belts. LCPs are also well-suited for computer fans, where their high tensile strength and rigidity enable tighter design tolerances, higher performance, and less noise, albeit at a significantly higher cost.[17][18]
Trade names[edit]
LCP is sold by manufacturers under a variety of trade names. These include:
- Zenite
- Vectra
- Laperos
- Zenite 5145L is a liquid crystal polymer with 45% glass fiber filler, originally developed by DuPont, which is used for injection molded parts with intricate features. Typical uses include electronic packaging, housing. etc. The heat deflection temperature is 290 °C. Relative Temperature Index (RTI considering strength but not impact or flexing) is 130 °C. The density is about 1.76 g/cm3. The typical tensile strength at room temperature is 130 MPa (19 ksi). Melting temperature 319 °C. The Deflection Temperature Under Load (DTUL) is 275 °C.
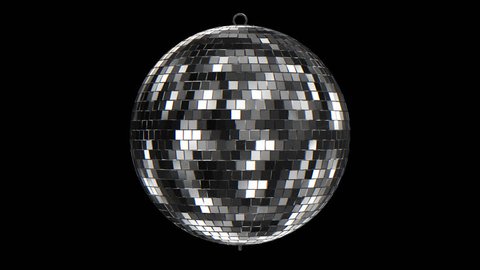

No comments:
Post a Comment